Precast concrete vs. cast-in-place: Pros and Cons
Precast Concrete and Cast-In-Place
As a seasoned
concrete contractor with over a decade of experience in
concrete installation, I understand the importance of selecting the right type of concrete for your construction project. The two prevalent methods—precast concrete and cast-in-place concrete—each offer unique benefits and limitations. Understanding these can help you make an informed choice tailored to your project's specific needs.
Precast Concrete: Manufacturing Precision and Efficiency
Precast concrete is a form of construction material produced in a factory setting, under strictly controlled conditions. This method entails creating molds of structural elements like walls, columns, beams, and stairs. Concrete is poured into these molds and cured in a regulated environment before being transported to the construction site for assembly.
Pros of Precast Concrete
- Quality and Durability: With precise environmental control, precast concrete usually achieves higher strength and durability than its cast-in-place counterpart. It is highly resistant to wear, tear, fire, and severe weather conditions.
- Time Efficiency: Precast concrete components are manufactured concurrently with site preparation, streamlining the construction timeline. Additionally, adverse weather conditions hardly impact the production or assembly process, ensuring on-time project completion.
Cons of Precast Concrete
- Cost: The initial expenditure for precast concrete is higher because of the controlled manufacturing environment, quality tests, and the logistics involved in transporting the elements to the site.
- Limited Customization: The factory-made nature of precast elements means that customization on-site is not possible. The molds are predetermined, limiting the architectural flexibility in terms of shape and size.
Cast-in-Place Concrete: On-Site Versatility
Cast-in-place concrete, as the name suggests, is mixed, poured, and cured right at the construction site. This method is especially popular for constructing foundations, floors, and other horizontal structures that require seamless connections.
Pros of Cast-in-Place Concrete
- High Customizability: One of the most significant advantages is the ability to create custom shapes and sizes on-site, perfect for intricate designs or structures with many curves and angles.
- Cost-Effectiveness: Generally, cast-in-place concrete incurs lower upfront costs compared to precast concrete. The reason is that it eliminates the need for factory manufacturing and subsequent transportation.
Cons of Cast-in-Place Concrete
- Time-Consuming:
The on-site curing process can take several days, which could prolong the construction schedule.
- Weather Dependency: Cast-in-place concrete is vulnerable to environmental factors. Any sudden change in weather can compromise the strength and quality of the concrete.
The Final Verdict
The choice between precast and cast-in-place concrete depends on your project’s specific needs. If your construction requires rapid, weather-independent, and robust structural elements, precast concrete is the apt choice, albeit at a higher cost. On the flip side, if your project prioritizes customization, and budget-friendliness, and is less time-sensitive, cast-in-place concrete will serve you better.
Regardless of the method chosen, partnering with a reputable concrete contractor is essential for optimal outcomes. An experienced professional will guide you through the decision-making process, ensuring that the structural integrity and aesthetics of your project are preserved.
Here at my
Sierra Vista Concrete Company, we specialize in concrete installation, including the installation of precast concrete panels and other components. If you are planning a construction project, please do not hesitate to
contact us for all your concrete needs!
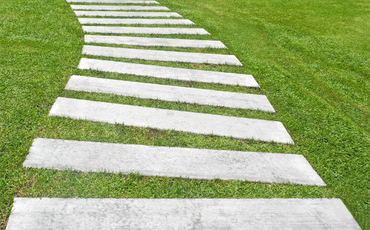
Like This Post? Share It...
You might also like
Blog of Sierra Vista Concrete
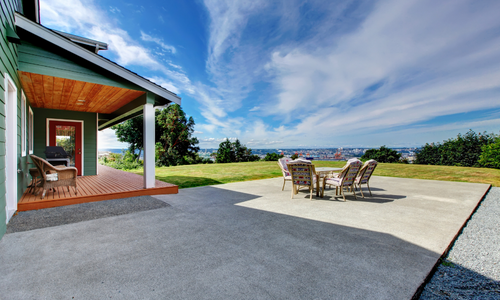

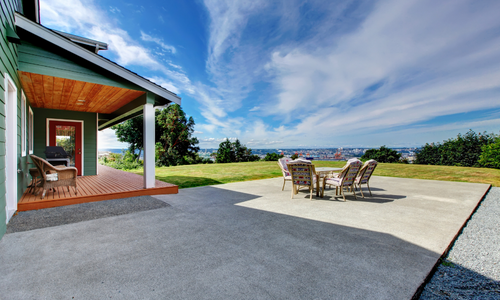